 |
Navigation directory |
|
 |
|
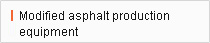 |
|
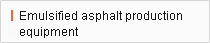 |
|
 |
|
 |
|
 |
|
 |
|
 |
|
Address:Industrial Park B the Xishan District YANGJIAN town District, Wuxi City, Jiangsu Province, Fuyang Road 22
Tel:0510-88720600
Fax:0510-85602472
Phone:13306174000、
18626300666、
13812188800、
13812188880
Contact:Mr lu
Web:www.guanxing.cn
www.giemco.com
E-mail:wxguanxing@163.com |
|
|
|
Home News News |
|
The autoclave sealed principles and new structural features |
| The traditional autoclave with double mechanical seal defects enamel reactor enamel reactor enamel reactor the stirring shaft enamel reactor generally supporting cantilever axis, the axis with a stirrer. Rotation due to the resistance of materials, shaft under heavy load at low speed rotation of swing much so that seriously affect the performance of the mechanical seal. Especially when the reactor pressure greater than 2.5MPa, Kettle mechanical seal on the design and manufacture of a greater degree of difficulty.
Commonly used double mechanical seal in actual use is often the result is not ideal, this structure of mechanical seals in reactor main the following disadvantages reactor stirring shaft general swing, the structural mechanical seal can not be a good solution to this problem, The lead seal likely to fail.
The axis of the pendulum will make static ring O-ring squeezed rotten; drive pin bend or twist off; snap ring shaft deflection is stuck lose floatabiligy; the moving ring sealing surface is premature strained;
The reactor pressure greater than 2.5MPa, the spring seat adapter screw slippery lead to seal failure; To this end, the structure of the mechanical seal must also set the sleeve, otherwise the spindle set screws slip scratch scrapped. The other does not set the sleeve axis swing the shaft the passive ring O-ring wear; must be imported from the A input is higher than the medium pressure coolant. Therefore, the mechanical seal of the institution must configure the high-pressure coolant circulation system, and increased investment. Are generally equipped with a high-pressure fluid cooling circulation system; requirements increase due to the high pressure of the cooling liquid, the entire sealing cavity.
Seal cavity, the sleeve and mechanical seal assembly must be designed into a set of mounted, increases the cost; the mechanical seal of this structure can not adjust the load coefficient k is too small, the end surface than the pressure P = Ps + (k-0.5) Pi, the structure k is generally not less than 0.6, due to media pressure Pi, the end face of ultra-high pressure ratio, the first level of the seal friction wear serious, leading to short life of mechanical seals; complex the structural mechanical seal structure, installation and removal difficult.
In order to improve the mechanical seal floating adjustment gap sealing various parts need special attention. If the gap is too large snap ring and sleeve, move easily pushed rotten ring seal or squeeze off. If the gap is too small, prone to ring stuck. Ring and the spring seat on the stationary ring and sleeve of the gap, and all must be strictly controlled. The large reactor equipment, took over many factors that affect the quality of the installation, the technical level of the erector. Part of the requirement to install the mechanical seal parts of the reactor as well as mechanical seal with shaft manufacturing tolerances h8, the finish of 1.6.
End should be made of the angle and light repair install snap ring dense ring shaft (sleeve). Axis static shaking amount shall not be greater than 0.5mm. Radial wobble in the axis of the static ring shall not be greater than 0.5mm. Kettle mechanical seal installation requirements to meet the design requirements of parts within parts meet the drawing. Balanced mechanical seals automatically ring seal and snap ring sealed chamber should be 3-5mm gap. When installing stationary ring, the end face of the need to use a dial indicator alignment and end face axis vertical degrees allow 0.05mm. The compression spring by drawing permissible error 2mm. After installation will the nuts loosen before driving. After the installation of the mechanical seal should the empty run together more than 24 hours operation. Mechanical seal is perpendicular to the axis by a pair or several slide relative to the end face of the fluid pressure and compensation institutions elastic (or magnetic) role to maintain paste merger together with the secondary seal to achieve resistance leakage shaft seal device.
Top mechanical seal structure by the stationary ring (static ring) 1, the rotary ring (snap ring) 2, the elastic member 3, the spring seat 4, a tight set of screws 5, the secondary seal of the rotating ring and stationary ring auxiliary seals 8, etc. elements , the anti-rotation pin 7 is fixed to the stationary ring to prevent the gland 9 rotated. Rotating ring and stationary ring often also based on whether they have the capacity of axial compensation called compensation ring and non-compensation also.
The mechanical seal of fluid may leak through the A, B, C, D four channels. C, D leak path is the sealing between the stationary ring and the gland, the gland and the casing, and both are static seal. The B channel is a rotation between the ring and shaft seal, Friction & Wear, it is only able to follow the axial direction of the compensation ring to the movement of a trace amount of, in fact, still a relatively static seal.
Therefore, these leak path is relatively easy to block. Static sealing elements most commonly used rubber O-ring or PTFE V-ring, as a the compensation ring of rotating ring or stationary ring secondary seal, sometimes using rubber of both elastic element function, PTFE or metal bellows structure.
A channel is the end face of the rotating ring and stationary ring paste cooperate with each other to the relative sliding of the movable seal, which is the main seal of the mechanical seal device, but also the key to determine the performance and life of mechanical seals. Thus, the processing requirements of the seal faces is very high, the order to make the seal between the end faces at the same time maintaining the necessary lubricating film, must be strictly cavity prepared end surface of the pressure per unit area, the pressure is too large, difficult to form a stable lubricating film, will accelerate the end faces wear; pressure is too small, the increase of leakage. So, to get a good seal performance have enough life, we must ensure that the design and installation of mechanical seals, the end face of pressure per unit area value in the most appropriate range.
Mechanical seal and soft packing seal comparison, has the following advantages: ① sealing is reliable in the long period of operation, the sealing state is very stable, very small leak, according to rough statistics, the amount of leakage is typically only soft packing seal, 1/100; ② long service life in the medium of oil, water class, usually ranging from 1 to 2 years, or longer the chemical medium usually more than six months; ③ friction power consumption small mechanical seal friction power only soft packing seal 10% to 50%. | | |  |
|
|
|